Monday, February 24, 2014
Retro in Black and White
Lately it seems all my work is being done on mid-century pieces. I went up a few decades and
wandered into the 70s. Ah yes, the wonderful 70s. Great times.
But dreadful clothing and furniture! Behold the common dresser:

But these do clean up nicely!!!
I would like to give a shout out to Dionne over at The Turquoise Iris for this inspiration.
I saw one she did in black and white that was just beautiful! She always does such unique work.
I used a semi-gloss in both the white and the black. But I had the hardest time getting the top
to smooth out. I used a Sherwin Williams acrylic and painted at least 3-4 coats. Was not happy.
I sanded between coats but just could not get his smooth. So I completely sanded it off and started over.
This time I used a BM black. Much better.
The handles were sprayed with carbon mist and highlighted w/gold gilding wax.
And of course there always has to be a little surprise detail when you look behind the door.


Viola
Linking up at my fave parties!! :
Kammys Korner - Trash to Treasure Tuesdays
Domestically Speaking - The Power of Paint Party
The Shabby Creek Cottage - Transformation Thursday
Miss Mustardseed - Furniture Feature Friday
Redoux - Friday Link Up Party
Homespun Happenings - Rustic Restorations Weekend
Funky Junk Interiors - Saturday Night Special
1929 Charmer - Sundays Best Party
Knick of Time Interiors - Knick of Time Tuesday
Elizabeth and Co., My uncommon Slice of Suburbia,
Savvy Southern Style. Weds, Beyond the Picket Fence, PJH Designs
From my Front Porch to Yours, The 36th Avenue,
Between Naps on the Porch
The Dedicated House,-Mon
Redoux
FURNITURE MAKE OVERS before and after 1
All the wonderful BEFORE & AFTERS you are about to see look so amazing in person,
and the students that preformed the work were outstanding.

How many of you would like to attend a furniture makeover weekend?
Well the PR Guy here and the LNT Group in Merritt coordinated that exact thing,
and I was the chosen teacher.
![]() |
we added drawer stops, learned some bled blocking tips, and added a graphic transfer on this dresser |
18 students, some with multiple projects, 2 days, almost every tool I own,
and with years of experience we gotter done!
![]() |
it was stripped, cleaned, painted grey, clear waxed, then dark waxed. It is off to the upholster soon! |
The week before the class, students started to email photos and ideas of that they would like to do.
When this chairs BEFORE pic showed up George started to panic, but I wasnt worried in the least.
![]() |
vintage high chair painted in a cherry red was heading back to Prince George to be a display piece in a floral shop |
We traveled over 2 hours to get to our destination but some ladies traveled much farther to join us.
![]() |
simple vintage chair given a new life with a light turquoise spray, sanding, and waxing. |
We did lots of color mixing and I showed students how to thin and strain paint for spraying.
Any one who wanted to try their hand at using the paint gun could also try it out.
![]() |
coordinating wallpaper was added in the back and you can see more of the detail of this cabinet now that it is lighter |
We wallpapered and waxed, we stripped some pieces, we stained a few pieces,
we painted and polyed, but best of all ...

I had a blast running non stop repairing things, adding things, making suggestions,
and simply helping everyone leave with a beautiful new pieces of furniture they would be
proud to display in their homes.
and simply helping everyone leave with a beautiful new pieces of furniture they would be
proud to display in their homes.
Sunday, February 23, 2014
POTTERY BARN TRUNK look a like
The Rebecca is a lovely rustic trunk available at Pottery Barn for $669.78

This photo has been in my idea folder for some time and when I found this
well worn plywood box (shown below) I knew it was the right candidate for the project.

It has wonderful worn edges and unbelievable character.
The problem was it was too worn in places to look good and be safe to use everyday as a coffee table.
I started by removing some unnecessary bits

and quickly moved to cutting pine boards with 45 degree angles needed to trim the box.





I started to paint the new wood (and Georges drill) with a chocolate color
and sanded it through in areas.

Then I washed the whole piece with watered down ASCP Graphite before waxing the first time.

After getting a nice even look between the original wood and the new pine,
I washed it with a thick muddy beige to give it an even tone of age.

I installed some wonderful hinges across the back, a vintage catch in front,


and the original metal corner guards using some nail head trim.
I love the original trunk handles, unfortunelty there was only one when I found it.

BEFORE AFTER

POTTERY BARN MINE



Sharing with:
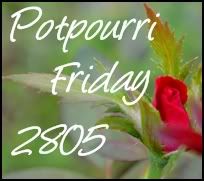
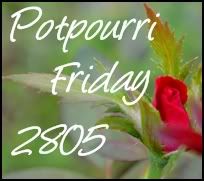
Little Frenchy nightstands
Found these little nightstands a few weeks ago and thought
I would spruce them up.
Did my own chalk paint in white and I used Ceces Vermont Slate
as an accent and on the handles. I also mixed some black paint with
some silver glaze to go over the slate.
I tried the wax paper method for this transfer from the "Graphics Fairy". Lemme just say that
wax paper does not mesh well with my printer! However, doing a little improvisation, I taped the wax
paper to a sheet of printer paper and got fine results! Be aware that once you start your transfer, be darn
sure of its placement! Once that paper touches anything the ink is transferred! Ask me how I know this.........Windex does a fine job of cleaning up any oops. Oh, and waxing or applying a topcoat will
smear the ink. I thought it would have dried after a day or two, but apparently it doesnt. So, I wiped it
down with water and was left with what you see above. These tops got an acrylic top coat.
Saturday, February 22, 2014
Getting A Handle On The Situation
Ive been restoring a Stanley Miter Box for a little while now. Its been my "get me through the winter" project. I picked it up from an local Antique and Thrift Store, an odd combination I know, its a thrift store with some area set aside for individual antique sales booths. We stop in every couple months and wade around. Id seen the miter box sitting there for the better part of a year but I didnt look too close at it until the booth was having a 25% off sale.

It wasnt the price that made me walk past it for so long, I almost felt guilty buying it at 25% off, it was the saw handle someone had cobbed on to it that caused my snobbish smirk. So now that Im hip deep in the restoration process, theres no doubt the old handle must go. It seems serendipity that days after I found the right handle pattern, the cold weather broke enough to get me back into my shop.
After reclaiming the shop and doing a little clean up and put away, I got to work on the new handle. I found a nice piece of cherry off-cut, a full inch thick and I got the handle pattern to fit perfectly over it. A little spray adhesive and I was ready to rock.
.JPG)
First thing was to drill out the marked holes. Bring on the Forstner bits and the drill press.

Then I took the block over to the bandsaw and removed a ton of the waste around the handle. I thought I was done so I took the tension off the saw blade and covered it back up. I used a coping saw to cut out the finger hole. I started taking some progress pictures and realized I had missed cutting out a section with the bandsaw.

I hate putting something away just to drag it out again so I opted for a different style of stock removal. I made a quick series of crosscuts with my carcass saw . . .
.JPG)
. . . and knocked the waste out of there with some chisel work. Now no one will ever be the wiser to my bonehead move, unless I write something about it online.

The I broke out my rasps and cleaned up all the saw cuts and chisel marks.
.JPG)
I made a point of turning the piece over regularly. I didnt want to get too fixated on the paint-by-number paper. Im glad I had it as a guide, but I wanted to make sure I paid attention to the wood and the handle itself and make something that would be comfortable and fit me well over something that followed all the exact lines of the mark up.
.JPG)
Then it was time for more rasp work. A heavy cut rasp to remove most of the stock followed by a finer smoothing rasp to bring it down to that touchable feel.

I worked my way around the outside and then hit the inner curves of the grip. Every few minutes I would pull the tote from the vise and test the feel in my hand. Then reclamp it and refine the curves until I was happy.

The paper template was marked with four holes for the saw nuts. I knew there was no way my saw plate would line up perfectly with those marks. They were close but not right. I had to be careful here because I knew from listening to my buddy Mark Harrell the "hang angle" of the handle is very important a saws function and usability. (Its saw-ability??).
Hang Angle is the relation between a saws toothline and the handle. Different saw geeks (like me) have different feelings about this relationship. It can be like rating beer with your buddies. I prefer a Cream Ale while John likes a Stout and Cindy likes Bocks. You get the idea. Matt Cianci at "The Saw Blog" has a great article that describes a saws hang better than I can, You can read it HERE.
Careful, you might find yourself falling down the same saw geek rabbit hole I have.
For my money I have always loved my Bad Axe Saws so I used my 12" carcass to help set the hang angle for the miter saw. I blocked it up so the plate rested on the handle and adjusted things until I was happy.

I marked out the location of the saw nut holes with a sharpie.

Then I set to drilling them both the through holes and the countersinks. The saw only came to me with one medallion saw nut and one regular one. A few years ago I picked up a couple of saw handles at a rummage sale. There was no saw plate attached, who knows what they did with that, but the nuts were there. One of those handles had three matching nuts that were brass like the medallion.

I had forgotten some of my reference material in the house and I couldnt remember which hole to use for the medallion. Instead of going in to get it, I used my iPhone for a quick image search of Disston miter saws and the first one I saw had the medallion in the lower back position. After I finished and came in the house I found my reference pictures had the medallion in the upper back position. So the saw is a little custom and a little different than standard. I guess Im OK with that.
I know you might say, "Why dont you just switch them?" but the back has the holes countersunk for the screw heads and the medallion head is bigger than the other three. Functionally I could re-drill the upper one and put the smaller nut in the over-drilled lower hole and things would be fine. But the smaller nut with the oversize countersink would mess with my Feng Shui. I couldnt deal with that, so Im happy to leave it as is.

All the saw nuts have the same patina, tough decision to leave them alone or shine them up.

OK, who am I fooling, of course Im going to shine them up.

The next step was to cut the kerf the saw plate would nestle into. I clamped the handle into my big wooden clamp and secured that to the benchtop.

I used a marking gauge from both sides to help make sure I set my saw line in the center of the handle.

Then it was just time to go to it with my small tenon saw.

Followed by some chisel and rasp work to clean a slot for the saws back.

After test fitting the saw plate and refining the fit of the kerf and the back notch I used a bit of sandpaper and a random orbit sander to take off the remnants of the paper template, spray adhesive, and other grime, oil spots, and crap the handle picked up in the process.

I sanded 120 grit and followed with a 220. I also hit the curves with some 220 by hand.

I applied a simple oil finish I like to use on shop pieces, Ive considered it for real pieces but it just seems like cheating to me.

After seeing the way the finish treated this cherry I might change my mind and "cheat" a little more often. Are you ready?
Its WD-40.
I spray it down heavy, (its still wet in the pictures) wait a minute or two, then wipe off the excess. I wait a few more minutes then I spray the piece down with a aerosolized, bees wax furniture polish and wipe that down.

Both products dry super fast and things are ready to handle almost right away. Ive found the treatment to be very durable and it has a great "feel" to it.
I joined together the handle and the saw plate, shiny saw nuts in place, and I was a happy puppy.

I have to spend some time with the toothline now, jointing and sharpening like you would expect, but that is no big deal to accomplish.

Whats left to finish this piece? Two big things. First remaking the wooden bed the stock "to be saw" rides on. That wont be a big deal. But the second thing is more challenging to me. There were several parts missing and instead of trying to buy them, or buy more older miter saws to get those parts, Ive decided to fabricate them myself. I can bend wood to my will, and Ive done some steel work before, but I always seem to run into some problem or frustration . We will see how it works out this time.
Until that time.
Ratione et Passionis
Oldwolf
Read More..
It wasnt the price that made me walk past it for so long, I almost felt guilty buying it at 25% off, it was the saw handle someone had cobbed on to it that caused my snobbish smirk. So now that Im hip deep in the restoration process, theres no doubt the old handle must go. It seems serendipity that days after I found the right handle pattern, the cold weather broke enough to get me back into my shop.
After reclaiming the shop and doing a little clean up and put away, I got to work on the new handle. I found a nice piece of cherry off-cut, a full inch thick and I got the handle pattern to fit perfectly over it. A little spray adhesive and I was ready to rock.
First thing was to drill out the marked holes. Bring on the Forstner bits and the drill press.
Then I took the block over to the bandsaw and removed a ton of the waste around the handle. I thought I was done so I took the tension off the saw blade and covered it back up. I used a coping saw to cut out the finger hole. I started taking some progress pictures and realized I had missed cutting out a section with the bandsaw.
I hate putting something away just to drag it out again so I opted for a different style of stock removal. I made a quick series of crosscuts with my carcass saw . . .
. . . and knocked the waste out of there with some chisel work. Now no one will ever be the wiser to my bonehead move, unless I write something about it online.
The I broke out my rasps and cleaned up all the saw cuts and chisel marks.
I made a point of turning the piece over regularly. I didnt want to get too fixated on the paint-by-number paper. Im glad I had it as a guide, but I wanted to make sure I paid attention to the wood and the handle itself and make something that would be comfortable and fit me well over something that followed all the exact lines of the mark up.
Then it was time for more rasp work. A heavy cut rasp to remove most of the stock followed by a finer smoothing rasp to bring it down to that touchable feel.
I worked my way around the outside and then hit the inner curves of the grip. Every few minutes I would pull the tote from the vise and test the feel in my hand. Then reclamp it and refine the curves until I was happy.
The paper template was marked with four holes for the saw nuts. I knew there was no way my saw plate would line up perfectly with those marks. They were close but not right. I had to be careful here because I knew from listening to my buddy Mark Harrell the "hang angle" of the handle is very important a saws function and usability. (Its saw-ability??).
Hang Angle is the relation between a saws toothline and the handle. Different saw geeks (like me) have different feelings about this relationship. It can be like rating beer with your buddies. I prefer a Cream Ale while John likes a Stout and Cindy likes Bocks. You get the idea. Matt Cianci at "The Saw Blog" has a great article that describes a saws hang better than I can, You can read it HERE.
Careful, you might find yourself falling down the same saw geek rabbit hole I have.
For my money I have always loved my Bad Axe Saws so I used my 12" carcass to help set the hang angle for the miter saw. I blocked it up so the plate rested on the handle and adjusted things until I was happy.
I marked out the location of the saw nut holes with a sharpie.
Then I set to drilling them both the through holes and the countersinks. The saw only came to me with one medallion saw nut and one regular one. A few years ago I picked up a couple of saw handles at a rummage sale. There was no saw plate attached, who knows what they did with that, but the nuts were there. One of those handles had three matching nuts that were brass like the medallion.
I had forgotten some of my reference material in the house and I couldnt remember which hole to use for the medallion. Instead of going in to get it, I used my iPhone for a quick image search of Disston miter saws and the first one I saw had the medallion in the lower back position. After I finished and came in the house I found my reference pictures had the medallion in the upper back position. So the saw is a little custom and a little different than standard. I guess Im OK with that.
I know you might say, "Why dont you just switch them?" but the back has the holes countersunk for the screw heads and the medallion head is bigger than the other three. Functionally I could re-drill the upper one and put the smaller nut in the over-drilled lower hole and things would be fine. But the smaller nut with the oversize countersink would mess with my Feng Shui. I couldnt deal with that, so Im happy to leave it as is.
All the saw nuts have the same patina, tough decision to leave them alone or shine them up.
OK, who am I fooling, of course Im going to shine them up.
The next step was to cut the kerf the saw plate would nestle into. I clamped the handle into my big wooden clamp and secured that to the benchtop.
I used a marking gauge from both sides to help make sure I set my saw line in the center of the handle.
Then it was just time to go to it with my small tenon saw.
Followed by some chisel and rasp work to clean a slot for the saws back.
After test fitting the saw plate and refining the fit of the kerf and the back notch I used a bit of sandpaper and a random orbit sander to take off the remnants of the paper template, spray adhesive, and other grime, oil spots, and crap the handle picked up in the process.
I sanded 120 grit and followed with a 220. I also hit the curves with some 220 by hand.
I applied a simple oil finish I like to use on shop pieces, Ive considered it for real pieces but it just seems like cheating to me.
After seeing the way the finish treated this cherry I might change my mind and "cheat" a little more often. Are you ready?
Its WD-40.
I spray it down heavy, (its still wet in the pictures) wait a minute or two, then wipe off the excess. I wait a few more minutes then I spray the piece down with a aerosolized, bees wax furniture polish and wipe that down.
Both products dry super fast and things are ready to handle almost right away. Ive found the treatment to be very durable and it has a great "feel" to it.
I joined together the handle and the saw plate, shiny saw nuts in place, and I was a happy puppy.
I have to spend some time with the toothline now, jointing and sharpening like you would expect, but that is no big deal to accomplish.
Whats left to finish this piece? Two big things. First remaking the wooden bed the stock "to be saw" rides on. That wont be a big deal. But the second thing is more challenging to me. There were several parts missing and instead of trying to buy them, or buy more older miter saws to get those parts, Ive decided to fabricate them myself. I can bend wood to my will, and Ive done some steel work before, but I always seem to run into some problem or frustration . We will see how it works out this time.
Until that time.
Ratione et Passionis
Oldwolf
Subscribe to:
Posts (Atom)